Injection molding materials
Injection molding uses a huge range of plastics, making it ideal for many applications across nearly every industry. we can source thousands of materials on request.
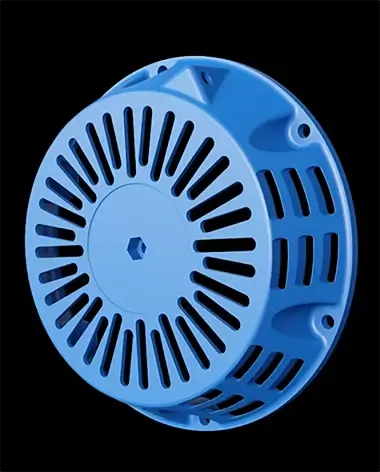
Acrylonitrile Butadiene Styren (ABS)
Polymethyl Methacrylate (PMMA)
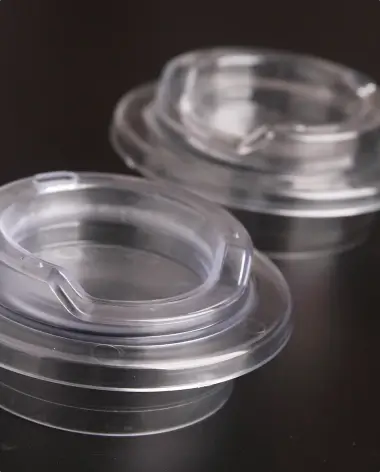
Polycarbonate (PC)
Polyethylene (PE)
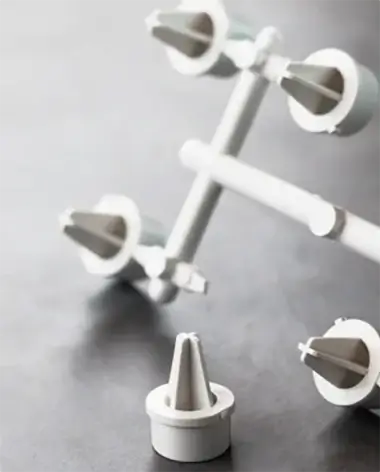
Polypropylene (PP)
Polyamide 6 (PA6)
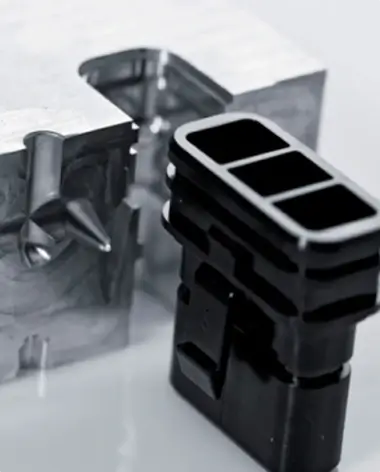
Polyether Ether Ketone (PEEK)
Polyoxymethylene (POM)